MACCHINE / ATTREZZATURE DI LAVORO IN SERVIZIO - analisi dei rischi
LE 6 FASI
DELLA SICUREZZA
1.
MAPPATURA
2.
AUDIT
3.
VALUTAZIONE
4.
GESTIONE DEL TRANSITORIO
5.
ADEGUAMENTO
6.
GESTIONE DEL CAMBIAMENTO
1) MAPPATURA
Censimento per
conoscere le attrezzature di lavoro, le loro caratteristiche ed
energie, e nel quale raccogliere i dati utili tra cui:
·
Identificazione: dati anagrafici, dati tecnici, presenza
documentazione, anno, marcatura CE, ecc.
·
Forme
di energia presenti: elettrica, aria compressa, oleodinamica,
termica etc..
·
Dispositivi di sicurezza / isolamento
·
Residui di processo etc..
In questa fase
si identificheranno le varie casistiche che possono verificarsi: es.
macchine che hanno subito modifiche sostanziali, macchine
autocostruite, marcate CE o meno, impianti, insiemi di macchine…
2) AUDIT
(verifica livello di conformità)
Verifica del
livello di conformità rispetto ai requisiti minimi di sicurezza
(es. vizi palesi con riferimento alla direttiva 2006/42/CE per
macchine CE, Allegato V D.Lgs. 81/08 per quelle non CE). Non si
tratta di un’analisi del rischio puntuale volta a definire le misure
di adeguamento eventualmente necessarie, quanto di una fase
necessaria a dare una priorità di intervento per un possibile
piano di adeguamento.
3)
VALUTAZIONE DEI RISCHI PER SINGOLA MACCHINA/ATTREZZATURA
Condurre sulle
macchine/attrezzature un’analisi di dettaglio per singola
macchina. Essa va condotta sui vizi palesi con riferimento ai
RES delle direttive europee per quelle marcate CE (per es. macchine
2006/42/CE) o ai requisiti minimi dell’Allegato V per quelle ante
CE. Vanno considerati i rischi presenti durante tutte le diverse
fasi di utilizzo di una macchina/attrezzatura: uso normale o
produzione, manutenzione, attrezzaggio o pulizia, ecc.
Tale fase
termina con la definizione delle misure di adeguamento.
4) GESTIONE
DEL TRANSITORIO
Spesso non è
possibile eseguire un piano di adeguamento sull’intero parco
macchine/attrezzature. La disponibilità finita di risorse richiede
la stesura di piani di miglioramento anche pluriennali; ciò
richiede comunque di attuare interventi immediati per la gestione
del rischio nel periodo transitorio tra cui:
·
procedure
·
messa
fuori servizio
·
formazione
·
ecc…
5)
PROGETTAZIONE E REALIZZAZIONE DI INTERVENTI DI ADEGUAMENTO
In base alle
priorità, l’azienda interviene con la
PROGETTAZIONE in
condivisione con gli operatori e la realizzazione INTERVENTI DI
ADEGUAMENTO.
6) GESTIONE
DEL CAMBIAMENTO
Gli interventi
effettuati sulle attrezzature di lavoro possono comportare dei
cambiamenti: installazione di protezioni, nuovi attuatori di
comando, nuove modalità di accesso alle zone pericolose, ecc…
La corretta
gestione delle modifiche/adeguamenti comprende:
·
redazione istruzioni e/o procedure specifiche
·
revisione schemi a corredo dell’attrezzatura
·
formazione e addestramento degli addetti sui rischi residui e
sull’utilizzo della attrezzatura
·
aggiornamento DVR
· aggiornamento
piano di manutenzione. Fa
parte integrante di una corretta gestione delle attrezzature la
verifica registrata di efficienza dei dispositivi con
funzione di sicurezza (es. arresti di emergenza, finecorsa di
interblocco, barriere ottiche)
Messa
a norma di macchine, attrezzature e impianti
Macchine usate, macchine installate,
cosa fare? Gli
infortuni sul lavoro connessi all’uso di macchine ed attrezzature
sono numerosi e spesso gravi. L’attenzione del legislatore verso le
problematiche della sicurezza delle macchine è stata sempre elevata.
Le norme, oggi vigenti, che regolamentano questo settore consentono
di assicurare livelli di sicurezza più che soddisfacenti. Non
sempre, però, analoghi livelli di sicurezza sono assicurati nelle
macchine di qualche anno fa. Da qui nasce l’esigenza del loro
adeguamento… di renderle più sicure… di avvicinarle alle nuove.
MACCHINE ANTECEDENTI L'OBBLIGO DI MARCATURA CE (ANTE 21.09.1996)
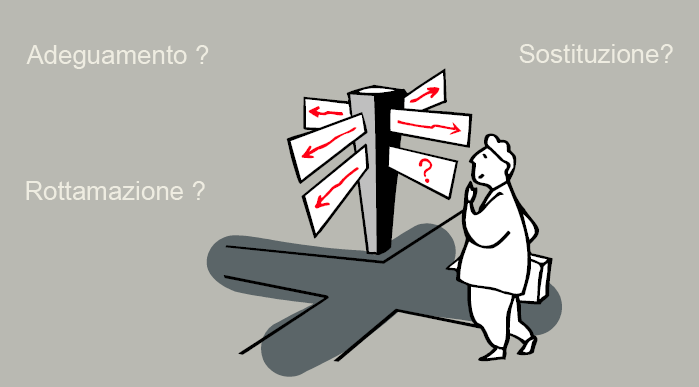
La giurisprudenza
conferma l’’orientamento interpretativo delle predette norme: «l’obbligo
di verificare costantemente, anche con il passare del tempo, la
rispondenza delle attrezzature di lavoro, rispetto all’epoca della
loro produzione, ai requisiti previsti dalla legge in tema di
sicurezza per i lavoratori (anche in conseguenza di innovazioni
normative ed aggiornamenti tecnologici), fino al punto di non
utilizzare l’attrezzo ove non sia possibile applicarvi apparati di
protezione».
Le ultime disposizioni legislative impongono al datore di lavoro
l’obbligo di far precedere l’adeguamento delle loro macchine da
un’attenta analisi dei rischi.
Vendita macchine usate
Chiunque venda una macchina o attrezzatura ad un
utilizzatore deve attestare la conformità della macchina alla
legislazione previgente. Ciò per effetto dell’art. 72 del D.Lgs.
81/08 (ed ex art. 11 del D.P.R. 459/56).
Di contro, una macchina priva di attestazione di conformità
rilasciata dal venditore non può essere acquistata per essere
utilizzata.
Che fare di una macchina non a norma di cui
ci si vuole disfare?
_ Permuta
In questa circostanza nell’atto di compravendita, a tutela del
venditore, è opportuno che questi specifichi che la macchina non
risulta in regola con le disposizioni di legge e che la sua
reimmissione sul mercato può avvenire previo intervento di
adeguamento alle norme di sicurezza.
L’obbligo di attestare la conformità della macchina alle norme
previgenti ricade pertanto sul rivenditore.
_ Cessione per conto vendita
Si ricade nel caso precedente
_ Rottamazione
Nessun adempimento ricade sul venditore, tranne di accertare che la
ditta acquirente sia autorizzata allo smaltimento di rifiuti.
_ Adeguamento
Le macchine devono essere sempre identificabili per cui è necessaria
la presenza di una targhetta di identificazione che riporti il nome
del costruttore, il modello e le caratteristiche principali
Percorso individuato da Studio
Valeri Vanni:
1. Censimento
attrezzature di lavoro con distinzione di tipologia e marcatura
(marcate CE e non marcate CE).
2. Verifica
della documentazione tecnica a corredo della singola attrezzatura.
3.
Identificazione dei pericoli ai sensi della direttiva macchine
2006/42/CE (per attrezzature marcate CE) e ai sensi dell’Allegato V
D.Lgs. 81/08 (per le attrezzature non CE) e valutazione dei rischi
(EN ISO 12100).
4. Stesura
piano di miglioramento con la definizione degli interventi.
5. In attesa
della messa a norma identificazione delle misure immediate di
compensazione del rischio: procedure, messa fuori servizio,
formazione ecc…
6.
Progettazione in condivisione con gli operatori e realizzazione
interventi di adeguamento.
7. Gestione dei
cambiamenti: aggiornamento della documentazione a corredo delle
macchine e attrezzature (dichiarazione conformità, manuale d’uso,
registro dei controlli e manutenzione) e aggiornamento della
valutazione dei rischi (DVR) con la gestione dei rischi residui.
8. Formazione
documentata degli operatori sui rischi residui e sull’utilizzo della
attrezzatura.
MACCHINE
ED ATTREZZATURE DI LAVORO: la sicurezza parte dall’acquisto.
Controllo in accettazione per l'acquisto: cosa deve controllare il datore di
lavoro
Consulenza
ed interventi per adeguamento delle macchine in servizio
(secondo il Titolo V del D.lgs. 81/2008 e direttiva 2009/104/CE)
REQUISITI
MINIMI DI SICUREZZA PER
L'USO DELLE ATTREZZATURE DI LAVORO
UTILIZZATE PER ESEGUIRE LAVORI IN QUOTA
PERIZIE ASSEVERATE, COMPRESE CONSULENZE
PER I TRIBUNALI
Consulenza
ed interventi per adeguamento delle macchine in servizio
(secondo il Titolo V
del D.lgs. 81/2008 e direttiva 2009/104/CE)
Scarica la guida sulle macchine in servizio
Sul
supplemento ordinario n. 108 alla Gazzetta ufficiale n. 101 del 30
aprile 2008 è stato pubblicato il
Decreto
Legislativo 9 aprile 2008, n. 81 recante “Attuazione
dell'articolo 1 della legge 3 agosto 2007, n. 123, in materia di
tutela della salute e della sicurezza nei luoghi di lavoro”.
Il nuovo decreto legislativo è composto da 306 articoli
(suddivisi in 13 titoli) e da 51 allegati tecnici. Dalla sua
entrata in vigore, ovvero dal
15 maggio 2008 sono abrogati:
·
il decreto
del Presidente della Repubblica 27 aprile 1955, n. 547;
·
il decreto
del Presidente della Repubblica 7 gennaio 1956 n. 164;
·
il decreto
del Presidente della Repubblica 19 marzo 1956, n. 303, fatta
eccezione per l’articolo 64;
·
il decreto
legislativo 15 agosto 1991, n. 277;
·
il decreto
legislativo 19 settembre 1994, n. 626;
·
il decreto
legislativo 14 agosto 1996, n. 493;
·
il decreto
legislativo 14 agosto 1996, n. 494;
·
il decreto
legislativo 19 agosto 2005, n. 187;
·
l’articolo
36 bis, commi 1 e 2 del decreto legge 4 luglio 2006 n. 223,
convertito con modificazioni dalla legge 5 agosto 2006 n. 248;
·
gli
articoli: 2, 3, 5, 6 e 7 della legge 3 agosto 2007, n. 123.
In
merito alle attrezzature di lavoro
il nuovo D. Lgs. 81-2008 si compone dei seguenti titoli:
·
Titolo I
- (art. 1-61) - Principi comuni (Disposizioni generali,
sistema istituzionale, gestione della previdenza nei luoghi di
lavoro, disposizioni penali)
·
Titolo
II …
omissis ….
·
Titolo
III
(art. 69-87) - Uso delle attrezzature di lavoro e dei dispositivi
di protezione individuale (Uso delle attrezzature di lavoro, uso
dei dispositivi di protezione individuale, impianti e
apparecchiature elettriche)
·
Titolo
IV …
omissis ….
·
Titolo V
… omissis ….
·
Titolo
VI …
omissis ….
·
Titolo
VII …
omissis ….
·
Titolo
VIII …
omissis ….
·
Titolo
IX …
omissis ….
·
Titolo X
… omissis ….
·
Titolo
XI
(art. 287-297) - Protezione da atmosfere esplosive
(disposizioni generali, obblighi del datore di lavoro, sanzioni)
·
Titolo
XII
(art. 298 - 303) - Disposizioni diverse in materia penale e di
procedura penale
·
Titolo
XIII
(art. 304 - 306) - Disposizioni finali
APPROCCIO PREVISTO PER IL SERVIZIO
La valutazione del rischio
rappresenta indubbiamente l'aspetto di maggiore innovazione
dell'intero impianto normativo, attorno alla quale tutto il sistema
ruota e da cui discendono gli ulteriori adempimenti posti a carico
dei destinatari della normativa. Si traduce nella redazione di
un documento scritto da custodire presso l'azienda.
In sintesi, si tratta di una individuazione generale di tutte
le possibili fonti di rischio “per la sicurezza e la salute
dei lavoratori” derivanti dall'espletamento di una determinata
attività lavorativa, anche se non richiedente l'utilizzo di
particolari prodotti di per sé pericolosi, valutata nel suo
complesso, per così dire "integrata" e non singolarmente
considerata.
La norma enuclea tre componenti imprescindibili del documento:
1.
l'individuazione dei rischi
(e i criteri adottati per il loro accertamento),
2.
le
misure di prevenzione e di protezione e i dispositivi di
protezione individuale adottati all'esito della valutazione per
eliminare o ridurre i rischi esistenti
3.
il programma delle misure ritenute opportune
per assicurare il miglioramento nel tempo dei livelli di sicurezza.
La valutazione del rischio costituisce un obbligo inderogabile, da
effettuarsi sempre e comunque, anche laddove la realtà lavorativa
sia tale da escludere la sussistenza di rischi specifici: il
datore di lavoro è tenuto ad effettuare la valutazione anche e
soltanto al fine di escludere la sussistenza di rischi e,
quindi, della necessità di procedere alla loro eliminazione o
riduzione.
L’insieme delle prescrizioni richiamate sopra comporta la necessità
che il datore di lavoro effettui i seguenti adempimenti:
-
Metta a norma le
attrezzature presenti in azienda e ogni nuova
attrezzatura che intende mettere a disposizione dei
lavoratori senza esclusione delle macchine marcate CE.
-
Realizzi procedure di lavoro omogenee
per organizzazione e scrittura che consentano ai lavoratori di
utilizzare in sicurezza le attrezzature indicando in
particolare quali sono i rischi residui connessi con l’uso
delle stesse.
-
Realizzi analoghe procedure per le fasi di manutenzione ordinaria
e straordinaria.
-
Realizzi procedure per la verifica periodica della sicurezza
delle attrezzature da parte degli operatori.
-
Indichi ai manutentori
(anche mediante un semplice elenco) quali ripari e sistemi di
sicurezza devono verificare nel corso della manutenzione
ordinaria.
-
Informi e formi il personale in
merito alle modalità di messa a norma
seguite e in merito all’applicazione delle diverse procedure di
lavoro.
In sostanza il cammino che l’azienda deve percorrere è
quello che segue:
Ø
Identificazione dei pericoli
e stima e valutazione dei rischi che le macchine presentano
allo stadio iniziale (incluse prove di emissione acustica, prove dei
sicurezza elettrica ecc.).
Ø
Identificazione delle situazioni da correggere in termini di
sicurezza.
Ø
Identificazione delle modifiche da effettuare e studio di
fattibilità delle stesse in funzione della riduzione del livello
di rischio, del rispetto di eventuali prescrizioni cogenti2 e della
funzionalità della macchina.
Ø
Progettazione delle modifiche
meccaniche e elettriche necessarie per la messa a norma (progetto di
massima e progetto esecutivo).
Ø
Messa in opera delle modifiche
(tipicamente aggiunta di ripari e correzioni all’impianto elettrico)
e collaudo funzionale delle medesime (collaudo di rispondenza al
progetto).
Ø
Verifica finale delle modifiche,
stima e valutazione dei rischi residui delle macchine e
certificazione o perizia di conformità.
CONTROLLO IN ACCETTAZIONE PER
ACQUISTO: cosa deve controllare il datore di
lavoro
(Clicca
qui per scaricare il documento)
(Clicca
qui per scaricare il documento: ACQUISTO DI MACCHINE)
Dal 21 settembre 1996 l’acquirente italiano che
non ottenesse la documentazione di cui ai
successivi punti, al momento della consegna di
una macchina da parte del costruttore o del
venditore, è obbligato a provvedere in
proprio a perfezionare, prima della sua "messa in
servizio", tutto quanto non fatto dal costruttore o
dal venditore inadempiente (d.lgs. 17/2010, art.2 comma 2, lettera
i) e art. 11, comma 1 del DPR 459/96).
I SERVIZI DI CONSULENZA RIGUARDANO, MA NON SONO LIMITATI A:
1.
Verifica contenuti dei
contratti di acquisto
2.
Verifica contenuti documenti di
accompagnamento delle macchine: dichiarazione CE di conformità
manuali d’uso, schemi etc…
3.
Verifica delle carenze palesi
presenti nella macchina
4.
Verifica delle condizioni e
delle caratteristiche specifiche del lavoro da svolgere, dei rischi
presenti nell’ambiente di lavoro, dei rischi derivanti dall’impiego
delle attrezzature stesse e dei rischi derivanti da interferenze con
le altre attrezzature già in uso
5.
Progettazione degli interventi
di bonifica inerenti: l’equipaggiamento elettrico, la parte
meccanica e l’aggiornamento della documentazione (schemi elettrici e
manuali d’uso);
6.
Validazione, ovvero verifica
degli interventi eseguiti comprendendo l’aggiornamento delle
relazioni per indicare lo stato d’arte raggiunto dopo gli interventi
di bonifica.
PERIZIE ASSEVERATE, COMPRESE CONSULENZE
PER I TRIBUNALI
Le perizie asseverate servono per andare a
verificare la reale rispondenza della macchina o
dell'impianto alle direttive e leggi assoggettate;
la perizia ha valore per la vendita di macchinari
usati e per l'acquisto di macchine tramite società
di leasing.
A seguito dei rilievi, si prospetta la
definizione
delle azioni correttive necessarie per
l'adeguamento della macchina.
Infine si procede con la stesura e consegna di
perizia asseverata sottoscritta dal Per. Ind. Valeri
Vanni, iscritto all'albo dei Periti Industriali di
Pesaro e Urbino ed in fase di iscrizione presso
l'albo dei Consulenti tecnici del Tribunale di
Pesaro e di Urbino.
|